Prusa i3 Pro
#Einleitung
Dieser Drucker ersetzt meinen AX1058 Drucker.
Der Prusa i3 ist ein sehr weit verbreitetes System, das macht in günstig aber auch ausgereift. Aus Kostengründen hab ich einen Bausatz erworben und musste den Drucker selbst zusammenbauen.
Anfänglich war ich noch etwas skeptisch, da bei diesem Konzept die Y Achse den ganzen Tisch bewegt und demzufolge bei steigendem Objektgewicht der Motor gegen arbeiten muss, da er es ja immer hin und her bewegt. Aber es scheint ja gut so zu funktionieren, sonst würde es nicht so viele davon geben.
Letztendlich ist es ein Set, das ich weiterempfehlen kann, auch wenn es ein paar Probleme gab.
Der Drucker hat einen Bauraum von 220x220x220 und ist leiser als mein erster.
Er wird über ein 12V 20A Netzteil betrieben.
#Aufbau
Der Aufbau hat rund 5h gedauert und war mangels "Zeit am Stück" auf mehrere Tage verteilt. Beim Aufbau gab es ein paar Probleme, zum Teil wurden auch Teile mitgeliefert, die nicht der Darstellung in der Aufbauanleitung übereinstimmten. Manchmal waren die Schrauben zu lang, manchmal waren sie zu kurz...
#Y-Achse
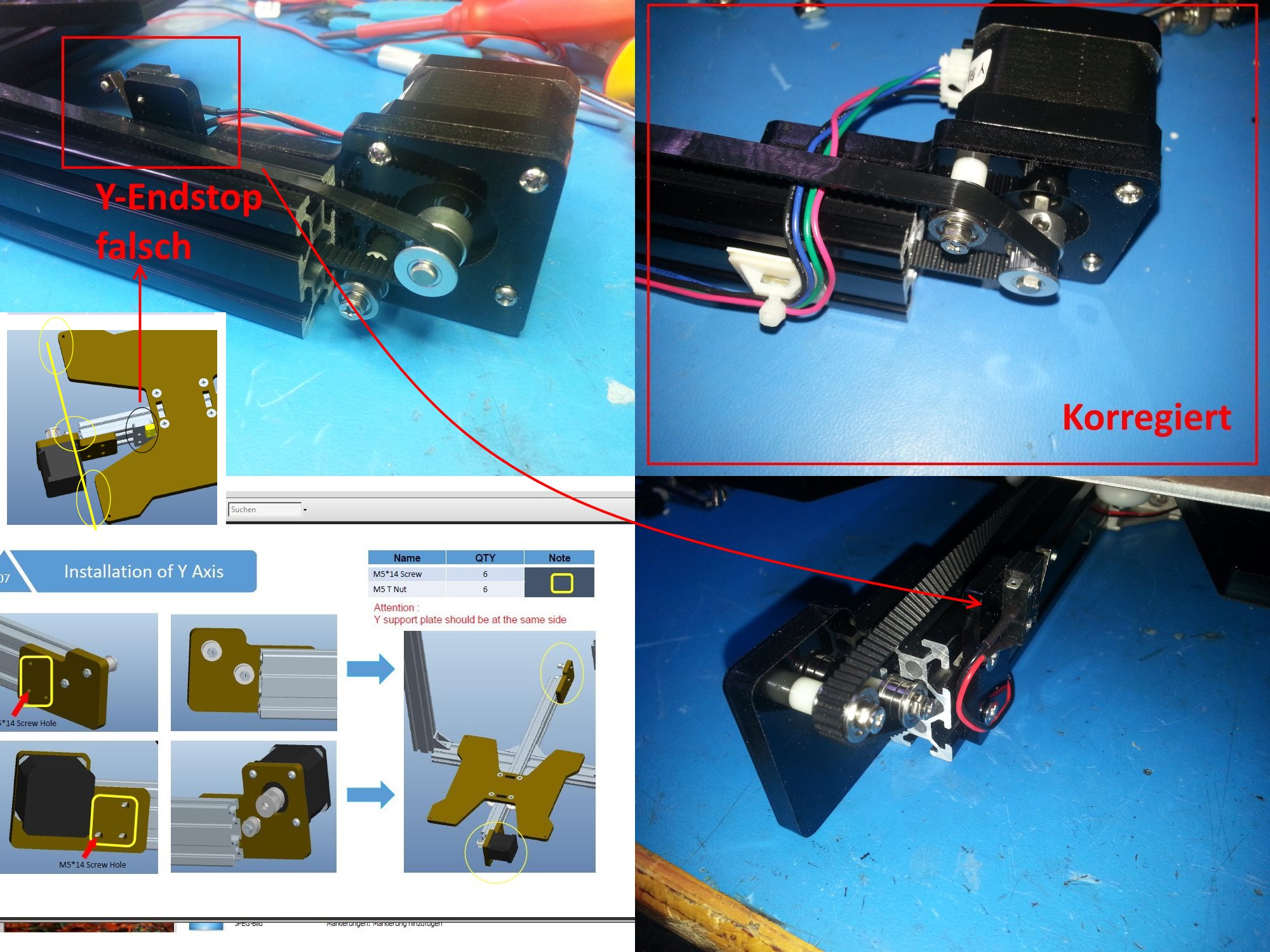
Hier ein Beispiel der Aufbauprobleme, durch andere Teile. Besonders unangenehm war die falsche Endschalterposition, weil ich die schon sauber verlegte Anschlussleitung wieder raus machen musste.
Man hätte natürlich auch die Verkabelung anpassen können, damit der Motor in die andere Richtung dreht. Aber letztendlich finde ich es auch recht angenehm, wenn die Platte zur Referenzfahrt ganz nach vorn kommt, so kann man während des Aufheizens noch die Oberfläche des Heizbetts behandeln (Klebestift, Haarspray und so weiter).
Wie auf den Bildern zu sehen ist, habe ich auf einer Seite den Zahnriemen gedreht. Das passierte aus einem einfachen Grund... es ist leiser. Wenn die Zähne nach innen zeigen wird bei jedem Zahnkontakt (oder besser gesagt dessen Außenkante) ein kleines Geräusch erzeugt. Durch die Verdrehung liegt der Riemen einfach nur auf und gleitet sehr viel leiser. Das gleiche hab ich später bei der X-Achse auch gemacht.
#Fertigstellung
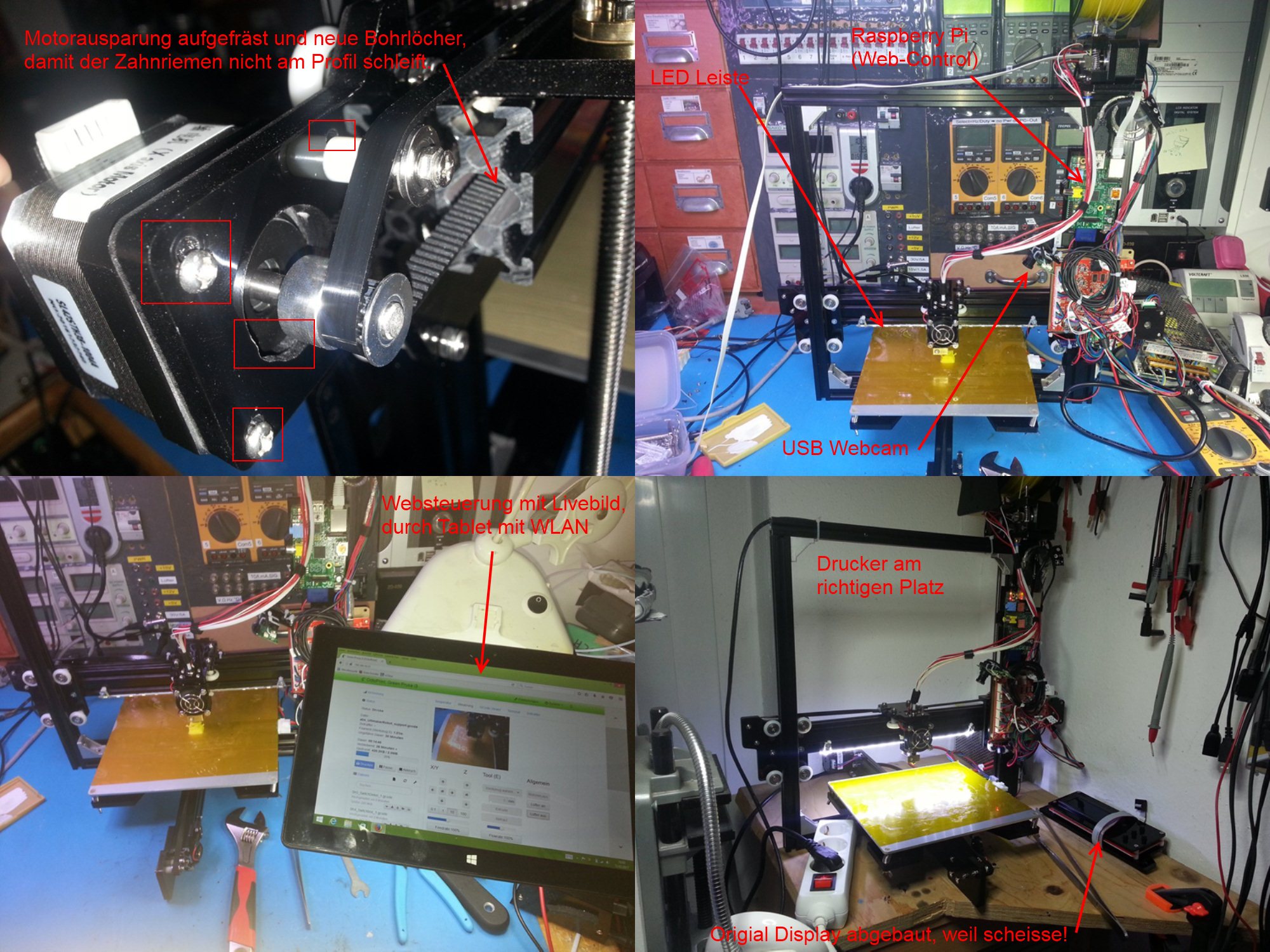
Die wohl größte Modifikation am Grundgestell musste für die X Achse gemacht werden, da das Teil tiefer ist als auf der Abbildung und der Transportriemen am Profil gerieben hätte.
Daher wurden die Bohrlöcher tiefer gesetzt und das Loch für den Motor musste ausgefräst werden.
Nach dem ersten Einrichten und erfolgreichen PLA Testdrucken, habe ich das Heizbett mit Kapton-Tape beklebt, da ich diesen Drucker bevorzugt für Materialien nutzen will, die der Kleine nicht schafft.
Außerdem musste ich bei der Verwendung des mitgelieferten Bedienpanels merken, dass es nur sehr rudimentär und langsam funktioniert. Darum hab ich nach den ersten Versuchen auch einen Raspberry Pi mit Oktoprint bestückt. So kann man die Achsen einfach über das Webinterface steuern, anstatt in den Untermenüs der Anzeige sich durch zu suchen. Eine Webcam sorgt jetzt dafür, dass ein Livebild die Druckersteuerung unterstützt. Die LED-Leiste ist an einen separaten FAN Anschluss angebracht worden. Dieser wurde eigentlich nicht belegt, lässt sich aber vom Webinterface durch eine Standardschaltfläche einfach ein und ausschalten. Die LED Leiste lässt sich so kurzzeitig einschalten, wenn man mal sehen will, wie es mit dem Druck so ausschaut.
#Extruder
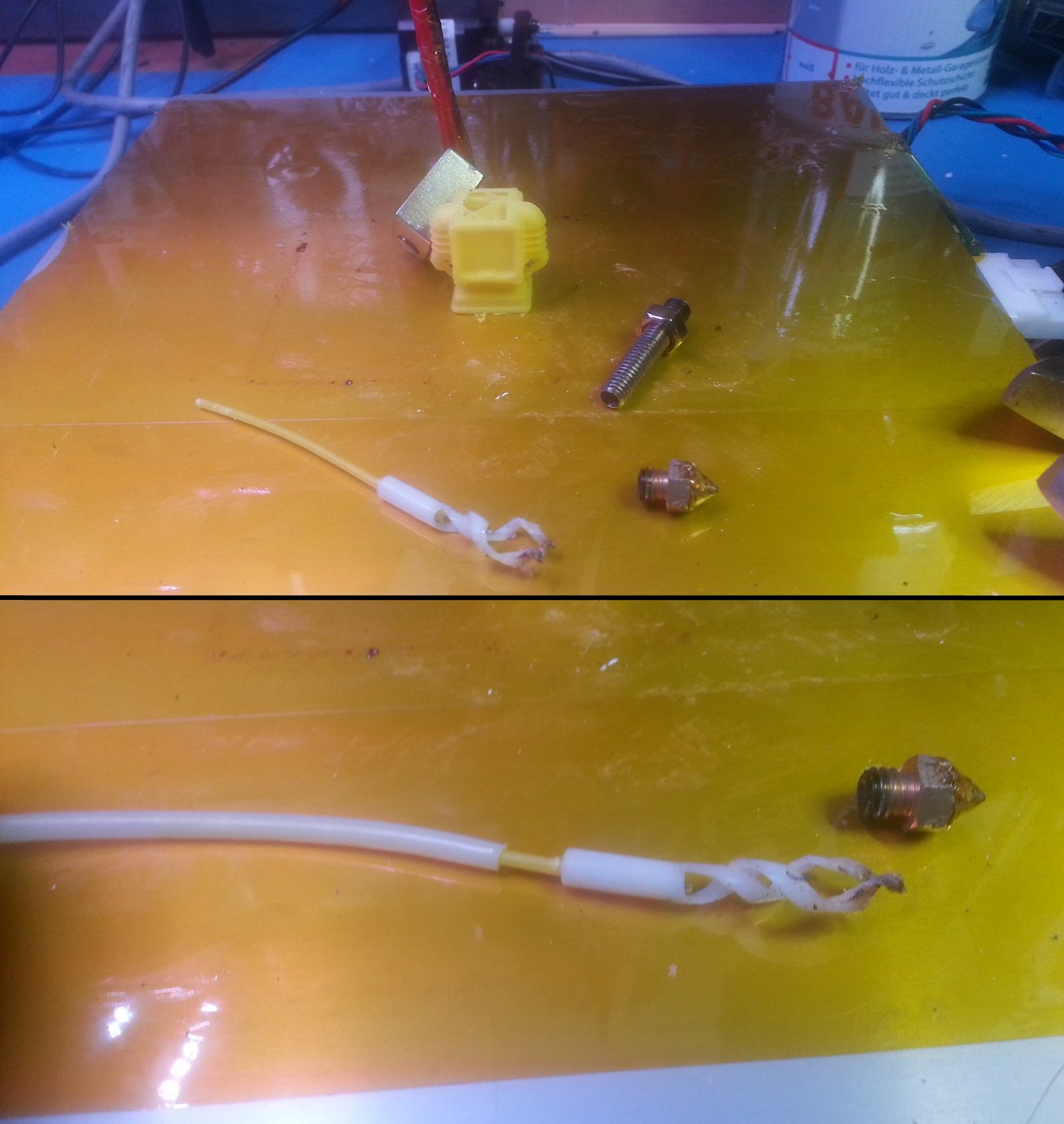
Beim Wechsel des Filaments zeigte sich wieder, wie schwierig das Einfädeln war, da der Draht im Extruder irgendwo hängen blieb. Ich könnte natürlich jedes Mal beim einfädeln den Draht anspitzen, aber... ne... das muss nun wirklich nicht sein.
Daher hab ich den Extruder zerlegt und festgestellt, dass der Übergang zwischen Bohrung und Gewindehülse unvorteilhaft ist. Ich hatte durch Besorgungen für meinen alten Drucker einen dünneren PTFE Schlauch da, mit 2mm Innendurchmesser.
Dieser ließ sich aber nicht direkt verwenden, da die Schlauchhalterung den kleinen Schlauch nicht erfassen kann und so das Material nicht geführt werden würde. Aber der kleine schlauch passt genau in den größeren mitgelieferten, allerdings war es nicht so einfach den da rein zu schieben.
Danach habe ich die Gewindehülse aufgebohrt, wodurch der PTFE Schlauch jetzt bis an das Hotend reicht.
Würde man das ohne den zweiten inneren Schlauch machen, dann würde die Querschnittsreduzierung fehlen, weshalb (vermutlich) leichter eine Verstopfung entstehen könnte, da das erwärmte Material nicht nur nach unten rausgedrückt wird, sondern auch seitlich bei der Zuführung nach oben.
Jetzt brauche ich den Draht nur noch oben beim Extrudermotor einfädeln und dann lässt es sich bis zum Hotend durchschieben. Der Außenschlauch reicht bis zum Anfang des Gewindebolzens, also knapp hinter dem Schlauchhalter. Aber der innere schlauch geht bis in die Spitze.
Das Ganze hat neben der leichteren Bedienbarkeit noch einen Nebeneffekt:
Da das Material jetzt durch den engeren Schlauch straffer geführt wird, kann ein geringerer Rückzug benutzt werden. Normalerweise würde der Rückzug erst mal den Draht innerhalb des Schlauches zurück ziehen, bis er schließlich beginnt Material aus der Spitze zu ziehen. Jetzt wird durch die engere Führung des Drahtes das Material schneller aus der Spitze gezogen, was vermutlich zu etwas sauberen Ausdrucken führen wird.
Zuletzt geändert am: Apr 14 2017 um 5:01 AM