Drucker AX1058
#Einleitung
Die 3D Drucktechnologie fasziniert mich schon seit längerem, aber ich hatte bisher weder die Zeit noch das Geld mich damit auseinander zu setzten.
Das ist nun anders, da ich mir für 500€ einen 3D Drucker geleistet hab.
Der Druckertyp ist unter folgenden Namen bekannt:
- Replicator (von Makerbot, wird nicht mehr hergestellt)
- Creator (von Flashforge)
- AX1058 (von CTC... den hab ich)
Ich vermute, der Replicator von Makerbot war das erste Seriengerät. Auf diesem basierend wurden die anderen 2 nachgebaut. Die Creator Serie von Flashforge sehen dem AX1058 mehr als nur ähnlich aus. Vieleicht stellt der eine es her und der andere packt einfach sein Label drauf. Ich tippe darauf, dass hier CTC die Dinger herstellt und Flashforge sein Label drauf knallt und sie untere einem anderen Namen anbietet. Auf den Bildern sieht der Drucker erst mal nicht so vertrauenerweckend aus, aber sie können doch so einiges. Und die Holzverkleidung ist doch sehr viel stabiler, als es auf den Bildern ausschaut (es wird Lasergeschnittenes 5mm Sperrholz verwendet).
Das Druckprinzip ist FFF (Fused Filament Fabrication) was im Grunde nur heißt, dass die Herstellung über einen zugeführten (Kunststoff-)Draht funktioniert.
Es gibt auch einige andere sehr interessante 3D-Druckverfahren, wobei das FFF Verfahren aber für den Hausgebrauch das vorerst Beste sein dürfte (relativ einfach, relativ präzise und relativ billig).
Nach einigen Modifikationen sind wohl auch schon Druckversuche mit Lötzinn geglückt (Info1 / Info2).
#Mein Drucker
Der Drucker kam in einem großen Paket, in dem viele Kartonteile den Inhalt gegen verschieben geschützt haben.
Der Doppelkopf war nur durch 2 Schrauben zu befestigen und schon sah er irgendwie einsatzbereit aus.
Allerdings war der eine Extruder höher als der andere, wahrscheinlich wurden sie beide einfach drauf geschraubt und fertig.
Wenn der Drucker abgeschaltet ist, lassen sich alle Achsen von Hand bewegen. So hab ich die Druckplatte bis unter die Extruder geschoben, um beide auf die gleiche Höhe einzustellen. Die benötigten 2 Inbusschlüssel waren mitgeliefert, genau wie ein paar Ersatzschrauben.
Die mitgelieferte Anleitung war für mich nutzlos. Sie beschrieb nämlich nur, wie man ein 3D Model zur Druckdatei umwandelt. Es war genaugenommen keine Anleitung für den Drucker sondern für die Software ReplicatorG... welche ich aktuell noch nicht benutzt habe.
#Mein erster Start
- Drucker auspacken
- Extruder aufschrauben
- Fehler: Blaues Band von der Druckplatte entfernt. Ich hab es für den Schutz der mit Kapton beklebten Druckplatte gehalten. Spätere Recherchen zeigten, dass es sich um eine Art Crepband handelt, das die Druckhaftung verbessert... Hier ein Vergleich beider Typen: Kapton tape vs. Blue painter’s tape
- Extruder auf die gleiche Höhe bringen
- Drucker mit Strom versorgen
- Im Menü des Druckers Adjust printig Base auswählen und den Anweisungen folgen (das ganze Menü ist auf Englisch).
- Filament laden (ebenfalls über Menüpunkt).
- Der Drucker heizt dann den eingestellten Extruder und gibt einen signalton, wenn er aufgeheizt ist. Dann wird auch der Motor gestartet und das Filament wird direkt eingezogen. Sobald unten was rauskommt kann man eine der Tasten drücken... der Motor stoppt und man beantwortet die Frage "Cancel Action" mit "yes"
- Mitgelieferte SD Karte reinstecken
- Den mitgelieferten Druckauftrag auswählen und starten
- Der Drucker druckt ein kleines Rechteck aus, welches nach ein paar 10-30 min fertig ist und begutachtet werden kann (die Angabe 10-30 heißt übrigens nicht, dass die Druckzeit variabel ist, sondern dass ich mich nicht mehr daran erinnere und es nicht extra nochmal testen will).
#Drucker und Betrieb
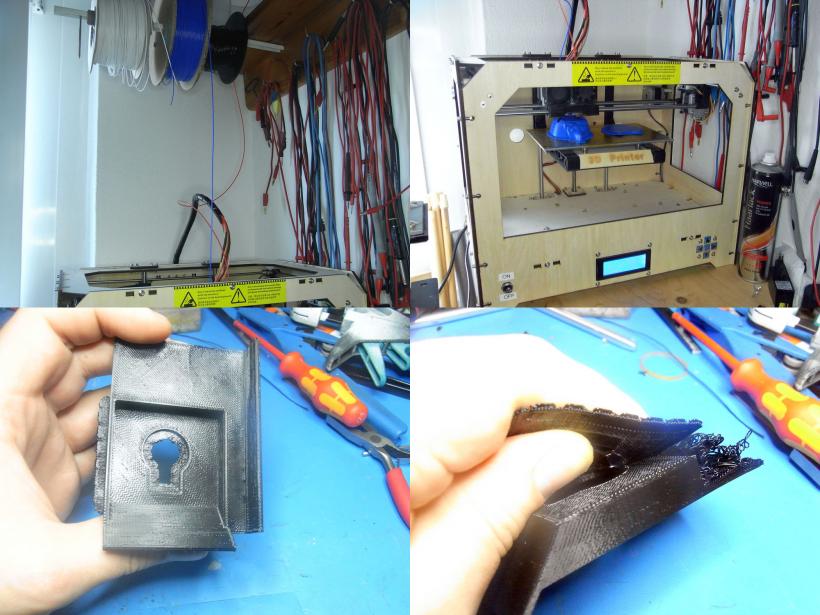
Die mitgelieferte Filamentrolle (1kg ABS Natur), habe ich nie wie vorgesehen angebracht.
Normalerweise wird sie hinter dem Drucker an 2 mitgelieferten Rollen aufgesteckt und das Filament über 2 Kunststoffschläuche in die Extruder geführt.
Bei meinen Recherchen hab ich irgendwo mal jemand gesehen, der die Rollen über dem Drucker auf eine Stange gepackt hat. Das war für mich auch die sinnvollste Variante, da sie einige Vorteile hat:
- Der Drucker ist aufgrund meiner Zimmerverteilung und der daraus folgenden Platzierung schlecht von hinten zu erreichen. An die Rollen über dem Drucker komm ich leichter ran.
- Durch direkten Blick auf die Rollen ist es leicht zu sehen, wann das Material ausgeht.
Wie auf den Bildern zu sehen, hab ich mir an der Vorderseite einen zusätzlichen Schalter gegönnt, weil der eigentliche Netzschalter neben dem Netzanschluss auf der Rückseite liegt und nicht so gut erreichbar war.
Der Drucker gibt ein Tonsignal (verschiedene Biep Signale) beim Starten und beim Ende des Druckvorgangs.
Das Tonsignal kommt noch nicht beim Starten des Druckauftrags, sondern erst dann, wenn er wirklich anfängt (also nach dem Aufheizen).
So weiß man auch aus größerer Entfernung, wann es los geht (und man vielleicht in kürze Material nachschieben muss) und wann er Fertig ist (damit man schnell den nächsten Auftrag starten kann und so die nächste Aufwärmphase verkürzt).
Während des Drucks hört man eigentlich nur noch die Motorbewegung und etwas leiser die Lüfter. Das kann (besonders bei kleinen zickzack Bewegungen) ganz schön rattern.
Verwendet werden hauptsächlich ABS (Acrylnitril-Butadien-Styrol) oder PLA (Polylactide).
Bei den unteren 2 Bildern sieht man einen Testausdruck in schwarzen ABS.
Gedruckt wurde mit Raft (eine Basisstruktur mit Sollbruchstellen). Unten links sieht man, wie sich das Raft ablösen lässt. Da ich ohne Stützstrukturen gedruckt habe, ist der eine Teil der mittleren Ebene ein bisschen in die Luft gedruckt worden, das sieht man von der Seite dadurch, dass die untersten Schichten (zum Raft hin) sehr viel stärker verbogen sind.
#2 Farbdruck
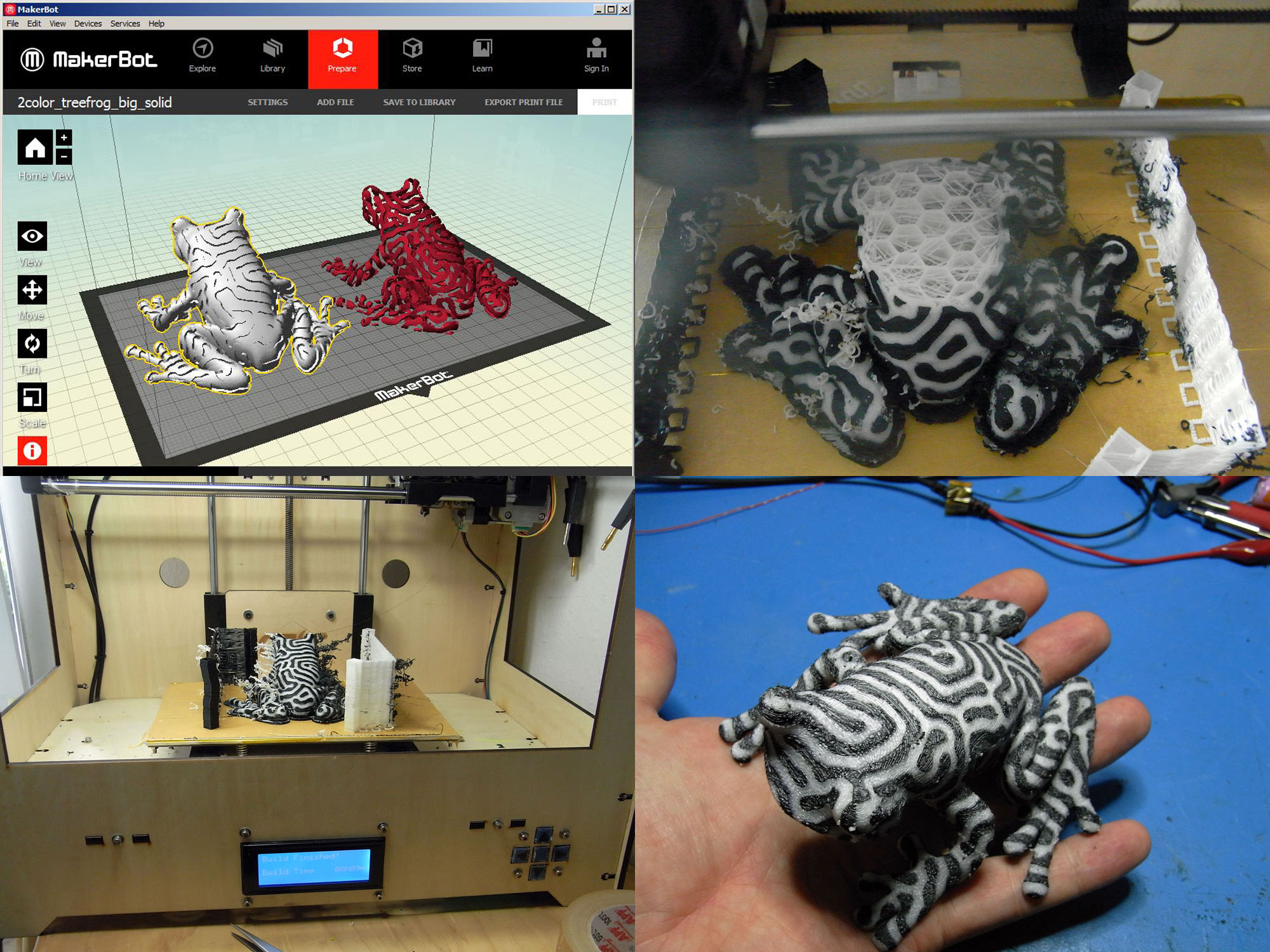
Der 2 Farbdruck ist einfacher, als ich gedacht hab.
In der Software (Makerware) kann ein einzelnes Objekt nach dem anwählen nicht nur skaliert, positioniert und gedreht werden, man kann auch festlegen, mit welchem Extruder das Objekt gedruckt werden soll.
So braucht man nur 2 ineinanderpassende Objekte in die Software laden und eines davon für den linken Extruder zum druck festlegen (Standard wird mit rechts gedruckt).
Im Bild sind beide Teile des Frosches nebeneinander verschoben worden, damit man es besser sieht.
Beide Dateien werden dann über die Software zu einem Druckauftrag umgewandelt.
Während des Ausdrucks wird bei jedem wechsel der Düse, eine farbige Struktur an der Seite mit gedruckt.
Ich gehe davon aus, das diese nur dazu da ist, die Düse für den unmittelbar bevorstehenden Druckprozess fertig zu machen. So ist viel Material in der Düse, welches nach wenigen Sekunden nach untern rauslaufen würde. Durch aus den Düsen laufendes Material (aus der die gerade nicht druckt) sind während des Drucks auch an beiden Seiten V Förmige ABS Fragmente direkt am Objekt. Diese gilt es zusätzlich zum Raft zu entfernen.
Wie unten auf dem Display gerade noch zu sehen, hat ein Objekt dieser Größe und Komplexität rund 8h gedauert.
#Nachbearbeitung
Wenn der Druck fertig ist, sind nicht selten Raft und Stützstrukturen zu entfernen. Die Oberfläche ist je nach Schichtdicke entsprechend uneben.
Was übersteht lässt sich natürlich mit einer Feile und einem Messer oder Skalpell relativ gut entfernen.
Für feine Nachbearbeitung bietet sich der Dampf von Aceton an:
- http://airwolf3d.com/2013/11/26/7-steps-shiny-finish-on-abs-parts-acetone/
- http://www.form3d.com/3d-druck-teile-aus-abs-mit-aceton-dampf-glatten/
Dadurch erhält man glatte und glänzende Oberflächen.
In einem kleinen verschließbaren Becher lässt sich auch Aceton mit ein paar ABS Rückständen aus früheren Ausdrucken zu einer Farbigen dünnflüssigen Masse verbinden. Das ABS löst sich im Aceton auf, wird aber nach dem trocknen wieder fest. So lässt sich die Masse, auch als Spachtelmasse und Kleber einsetzten.
#Druckfehler
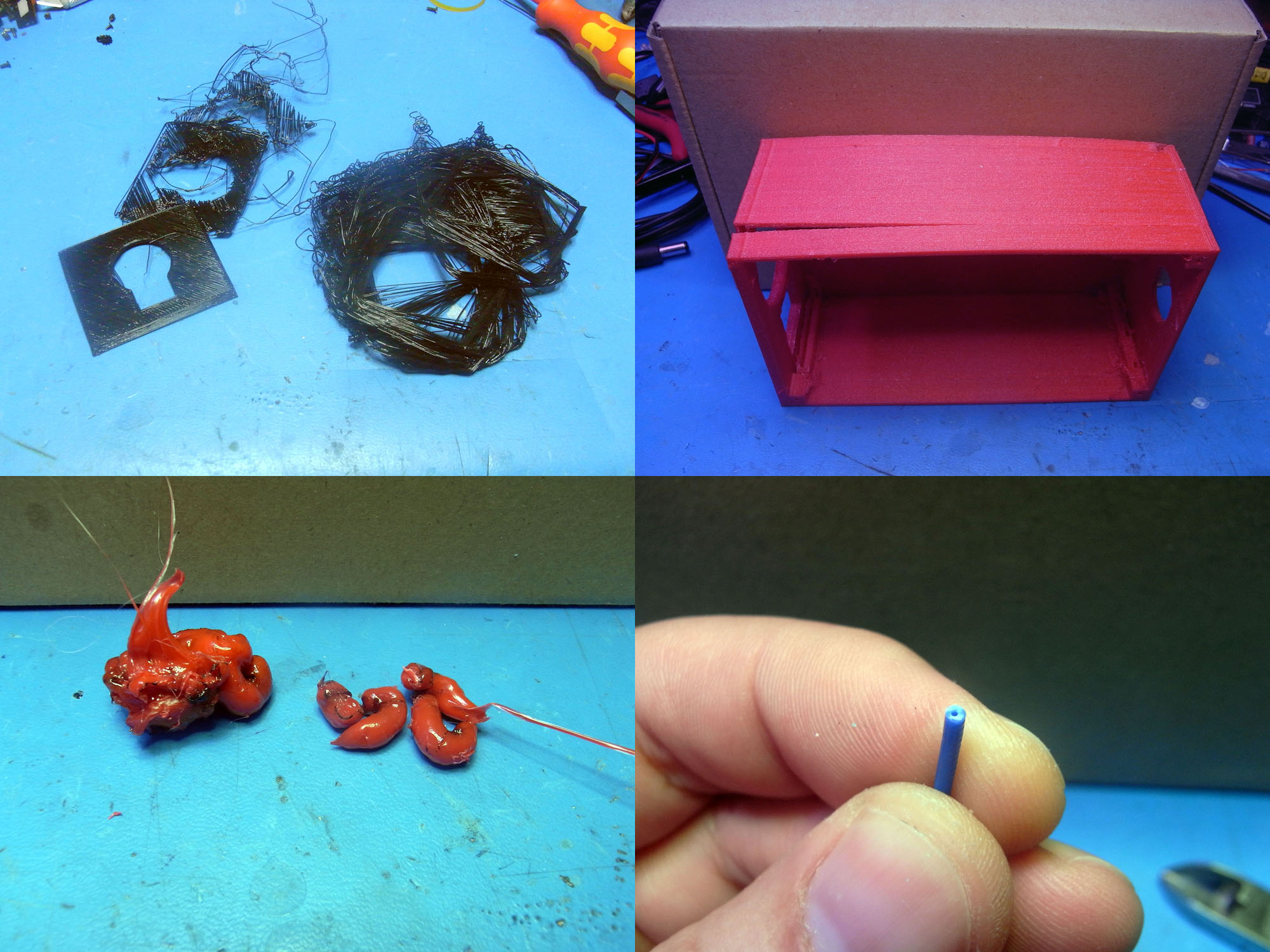
Zu geringe Druckhaftung
Das ist eines der höchsten Probleme, das auch andere wie "Warping" nach sich ziehen kann.
Beim Druck wird das Objekt ja Schicht für Schicht aufgetragen, wobei die neue Schicht mit der darunterliegenden verschmolzen sein sollte.
Problematisch ist es, wenn der Druckkopf gegen das Objekt fährt, das passiert z.B. bei:
- Warping (mehr dazu weiter unten)
- Einem fehlerhaft justierten Druckbett
- Einem 2ten Extruder dessen Druckkopf nicht das gleiche Level wie der aktuelle hat
Sobald der Extruder gegen das Objekt fährt, wird ein mechanischer Druck seitlich ausgeübt, der bei zu geringer Haftung das Objekt vom Druckfeld lösen kann. Genau das ist bei Bild:Druckfehler_ObenLinks passiert. Das Objekt hat sich von der Plattform gelöst und ich hab später dieses Ergebnis vorgefunden. Nachdem sich das Objekt gelöst hat, sind die darauf folgenden Lagen "in die Luft" gezeichnet worden, während das Objekt am Extruder geklebt hat und über das Druckbett mit geschliffen wurde.
Die Haftung kann mit Haarspray, oder nach meiner Erfahrung besser... mit der ABS+Aceton Mischung verbessert werden. Man lößt einfach ein paar Durckreste in Aceton auf. Die Flüssigkeit nimmt je nach Sättigung die Konsistenz von Honig an und hat die Farbe der verwendeten ABS-Reste, welche sich komplett drin auflösen. Wenn diese Mischung auf die kalte Druckplatte aufgetragen wird, trocknet das ganze gut ein und man erhält einen ganz leichten ABS Film auf der Druckplatte, welche sehr gut hält... so gut, das man danach Probleme beim ablösen bekommt. So ist das mit der Haftung... zu wenig ist schlecht, zu viel aber auch...
Warping
Hierbei kommt es zu mechanischen Spannungen, weil das ABS beim abkühlen sich verzieht. Wenn die Druckbetthaftung zu gering ist, können sich die Ecken nach oben wölben.
Wie im Bild:Druckfehler_ObenRechts zu sehen ist, führt ein Warping der Ecken auch dazu, dass bei dem Objekt die Eckmaße (Objekthöhe) anders sind als die Maße in der Mitte. Das ist dann kein Gehäuse mehr sondern eine Wippe.
Ein weiteres Problem beim warping... wenn sich die Ecken hoch wölben fährt der Druckkopf gegen. Das ist einerseits schlecht für die Haftung auf dem Druckbett, führt aber auch dazu, das Material vom Druckkopf wieder abgeschmolzen wird und wie im Bild:Druckfehler_UntenLinks sich zu Einzelbrocken formt.
Die kleineren sind bei früheren Ausdrucken entstanden und lagen dann im oder neben dem Objekt.
Der Große hat sich an der Düse gesammelt und hat den Thermosensor umschlossen... nach dem entfernen war einer der Drähte abgerissen und der Drucker meldete "Extruder overheat, check connections".
So ein Fehler ist zwar ärgerlich, aber nach dessen Korrektur kenn ich meinen Extruder besser als vorher ;)
Risse
Dieser Fehler entsteht einerseits durch die Materialspannung, die auch das Warpin hervorruft, aber auch durch schlechtes Filament.
Ich hab das billigste genommen, das ich finden konnte und wie in Bild:Druckfehler_UntenRechts gesehen werden kann, sind da Lufteinschlüsse drin. Wusste ich vorher nicht... aber man lernt ja dazu.
Jedenfalls funktioniert der Extruder recht einfach. Da ist ein Beheizter Metallteil (hotend) durch den ein PTFE (Teflon) Schlauch das Material führt, welches von oben über einen Schrittmotor und Zahnräder das Material zuführt. Das heißt für den Drucker:
- mach eine Lage von Volumen X
- dafür brauchst du die Menge Y an Material
- die werden durch Z Schritte am Motor zugeführt
Wenn Lufteinschlüsse im Filament sind, oder es zwischendurch mal einen geringeren Querschnitt hat, wird weniger Material zugeführt, als eigentlich gebraucht wird. Dadurch leidet natürlich die "Strukturelle Integrität" des Objekts und wenn jetzt noch die mechanischen Spannungen vom ABS durch das Abkühlen hinzukommen, dann kann es zwischendurch mal Knack machen und ein Riss ist drin.
#Ende
Leider hat in der Zwischenzeit mein erster 3D Drucker seine Funktionstüchtigkeit eingestellt.
Zuerst gab es ein paar Unfälle. Dann ein paar Reparaturen und letztendlich die Einsicht, dass es sich nicht lohnt hier weiter zu machen.
Die meisten Unfälle: Objekte lösten sich beim drucken vom Druckbett und klebten dann an der Düse, die weiterhin Material nachschob. Bei einigen Fällen legte sich das warme Plastik um die Anschlussleitungen von Sensor und Heizpatrone.
Als die Drähte der Heizpatrone abgerissen wurden, war nur noch ein kalter Plastikrest da.
Schlimmer ist aber eine Beschädigung des Temperaturfühlers. Dieser meldete eine zu geringe Temperatur und der Controller regelte entsprechend nach. Die Folge... das Hotend überhitzte, der farbige Kunststoff landete in schwarzen Tropfen auf dem Heizbett. Außerdem zeigte sich, dass die Zugkraft der beiden Extruder massiv abgenommen hat. Man kann relativ leicht die Motoren anhalten. Die 24V Spannung passt aber... vielleicht gab's bei einem der Unfälle auch eine Überhitzung und Schädigung der Motoren.
Da es noch ein paar grundsätzliche Probleme gab (Konstruktionsbedingte Verbiegung der Wellen) hab ich mich nach anderen Druckertypen umgesehen.
Zuletzt geändert am: Mär 26 2017 um 6:43 PM